Quality serves as the foundation of our AMHS solution product guarantee. The construction of a quality system and its continuous enhancement fortify quality management, boost company efficiency, bolster customer trust, and increase market share. Consequently, MeetFuture Technology has instituted a thorough quality and reliability assurance and control system to safeguard every stage from R&D to mass production.
Our production base features a 2000 m2 dust-free clean room, fully equipped for the installation, commissioning, calibration, and reliability verification of AMHS hardware equipment. We pledge to deliver high-quality products that earn our customers' trust. By actively engaging with customer feedback, we persistently advance and align with their expectations for standard processes, product quality, project delivery, and service excellence.
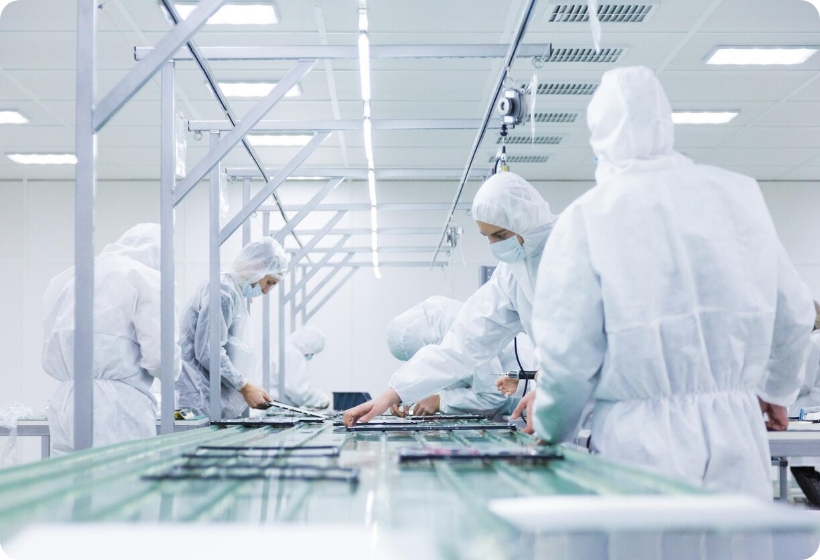
MeetFuture products are subject to a robust series of quality control measures and methods, ensuring that the equipment's quality during design, manufacturing, installation, commissioning, and usage aligns with the set standards. We implement a product life cycle quality control plan early in the APQP process. We maintain stringent quality oversight at each node. This approach enhances the equipment's reliability, safety, and user-friendliness, diminishes failure rates, extends service life, boosts production efficiency, and generates greater economic value for our customers.
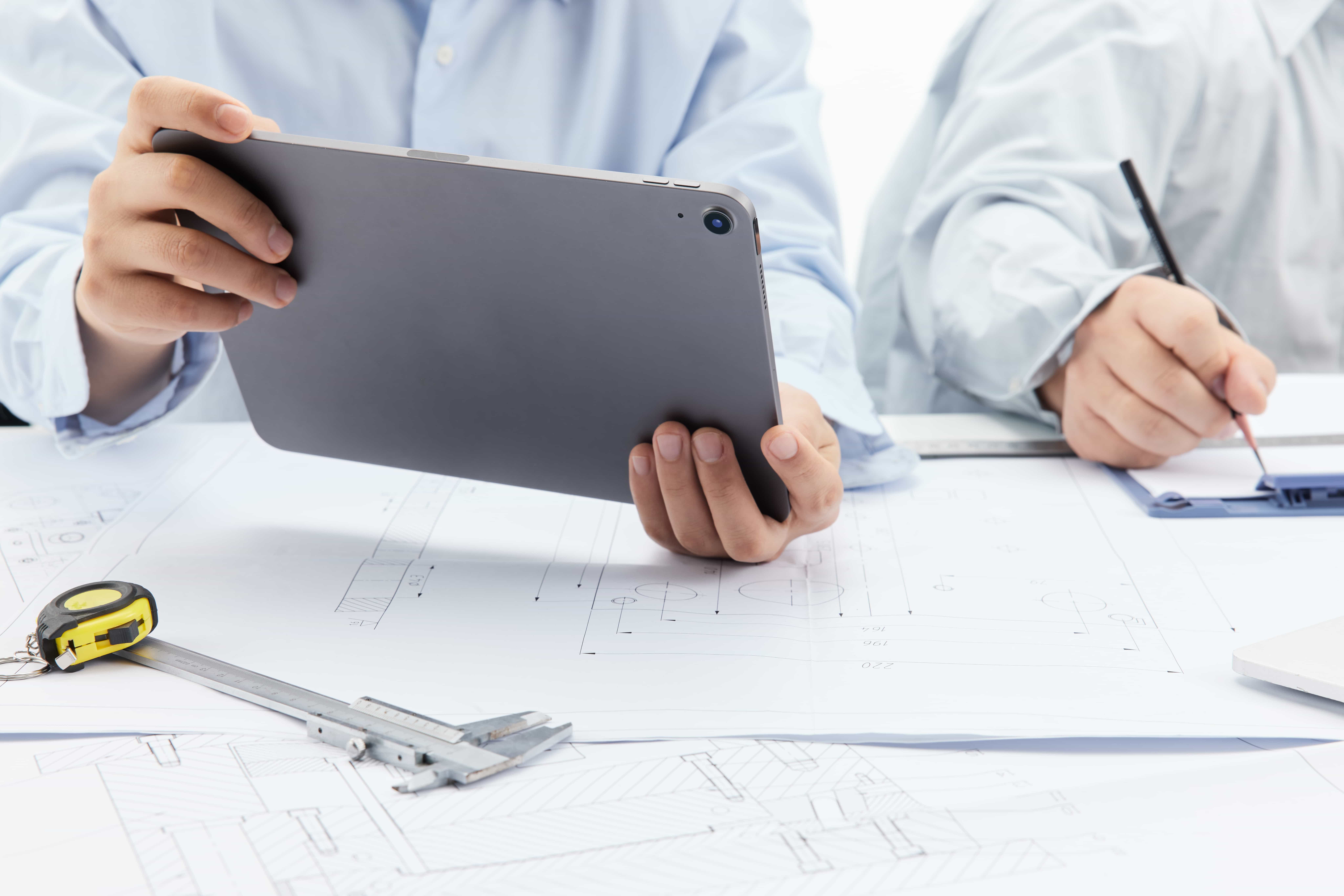
Design/Verification Review
Introduction of Quality Certification System for Mass Production
Quality Assurance System for Initial Mass Production
DFMEA/PDCA
Transport Reliability Test of AMHS Equipment
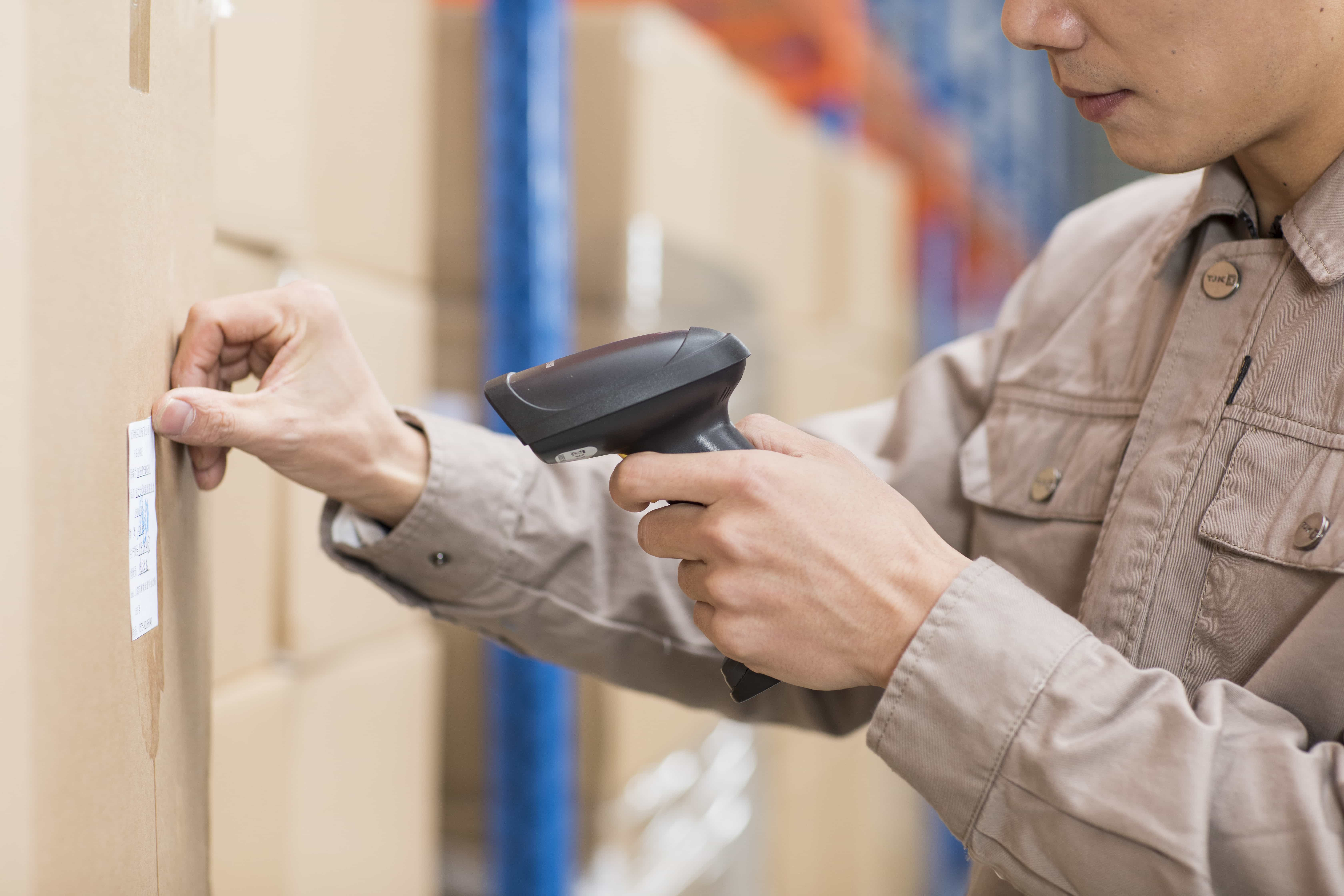
Excellent Supporting Cooperative Business
Ensure the Mass Production of Parts
Supplier Evaluation and Guidance
Product Assurance Activities
Check for Baseline Consistency
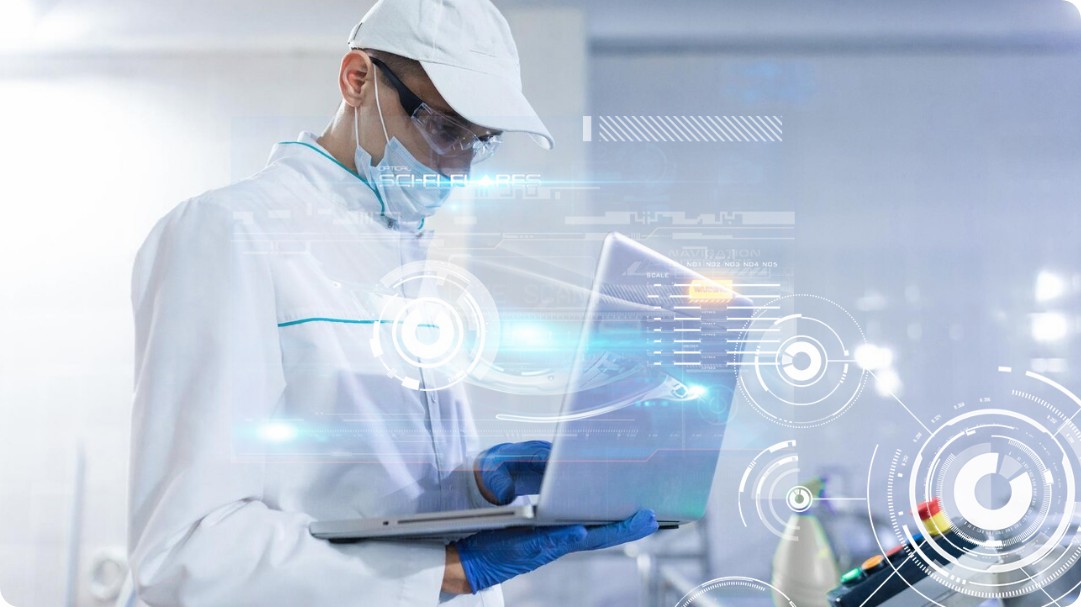
Manufacturing Engineering Standards
Standards Compliance
Forecast and Manage Potential Issues
Defect Improvement Activities
Process Parameter Management
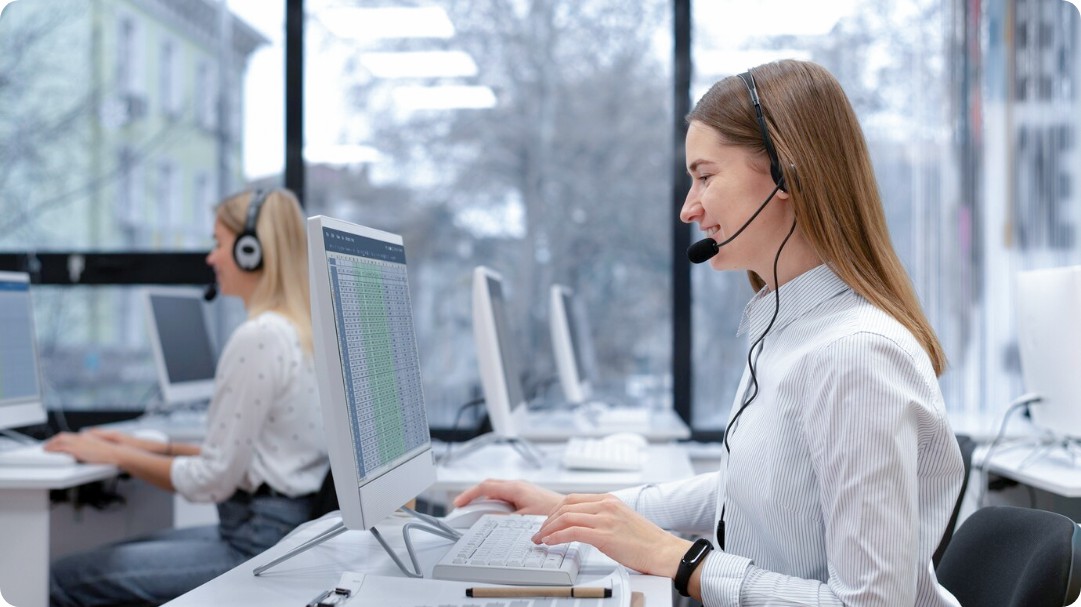
100% Performance Test of All Products
Technical Data Report TDR
Customer Complaint CLCA Management
Quality Meeting Review
Customer Satisfaction First Principle
Product reliability — the product's capacity to consistently perform its intended functions under specified conditions — is the fundamental criterion for assessing product quality. It is indicative of the product's stability, durability, and customer satisfaction. Key metrics include Mean Time Between Failures (MTBF), failure rate, reliability life, and failure modes. Through methodical reliability testing, MeetFuture Technology establishes a foundation for the stability and performance of products over their lifespan, ensuring all products meet or surpass customer expectations and industry benchmarks. Enhancing product reliability is instrumental in lowering maintenance expenses, prolonging product lifespan, and boosting market competitiveness.
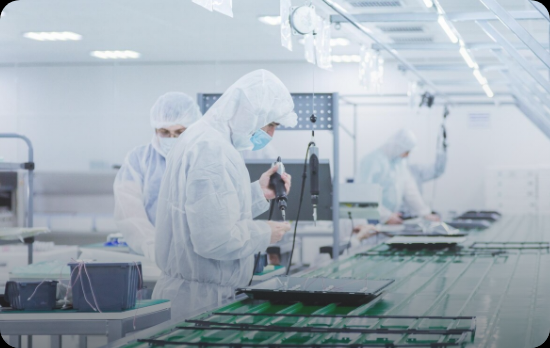
Reliability design is the proactive approach to ensuring product dependability, encompassing preventive design, cost-benefit analysis, and market competitiveness considerations. Design principles and methodologies, such as redundancy design, derating design, thermal design, environmentally conscious design, Failure Mode, Effects, and Criticality Analysis (FMECA), design reviews, reliability forecasts, and prototype testing, offer strategies to achieve high reliability standards from the outset.
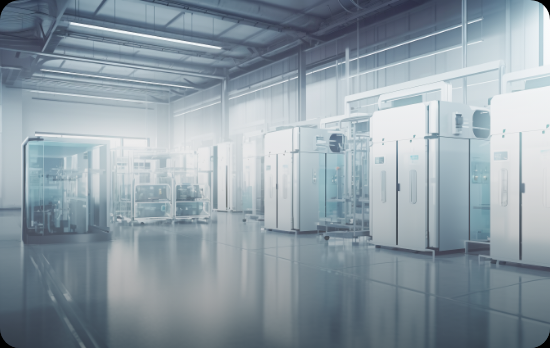
This includes procedures like Environmental Stress Screening (ESS), Accelerated Life Testing (ALT), and Highly Accelerated Life Testing (HALT). These tests are crucial for uncovering potential flaws during product development and production, assessing product lifespan and performance, and furnishing manufacturers with the data and insights necessary for product enhancement.
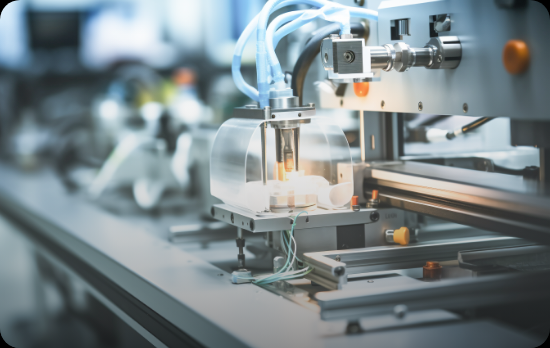
Environmental testing, encompassing temperature and humidity, vibration, shock, salt spray, and Highly Accelerated Life Testing (HALT), plays a crucial role in enhancing product reliability. These tests verify that products adhere to design specifications and performance criteria, forecast product lifespan, pinpoint potential flaws, and yield data that informs superior design practices.
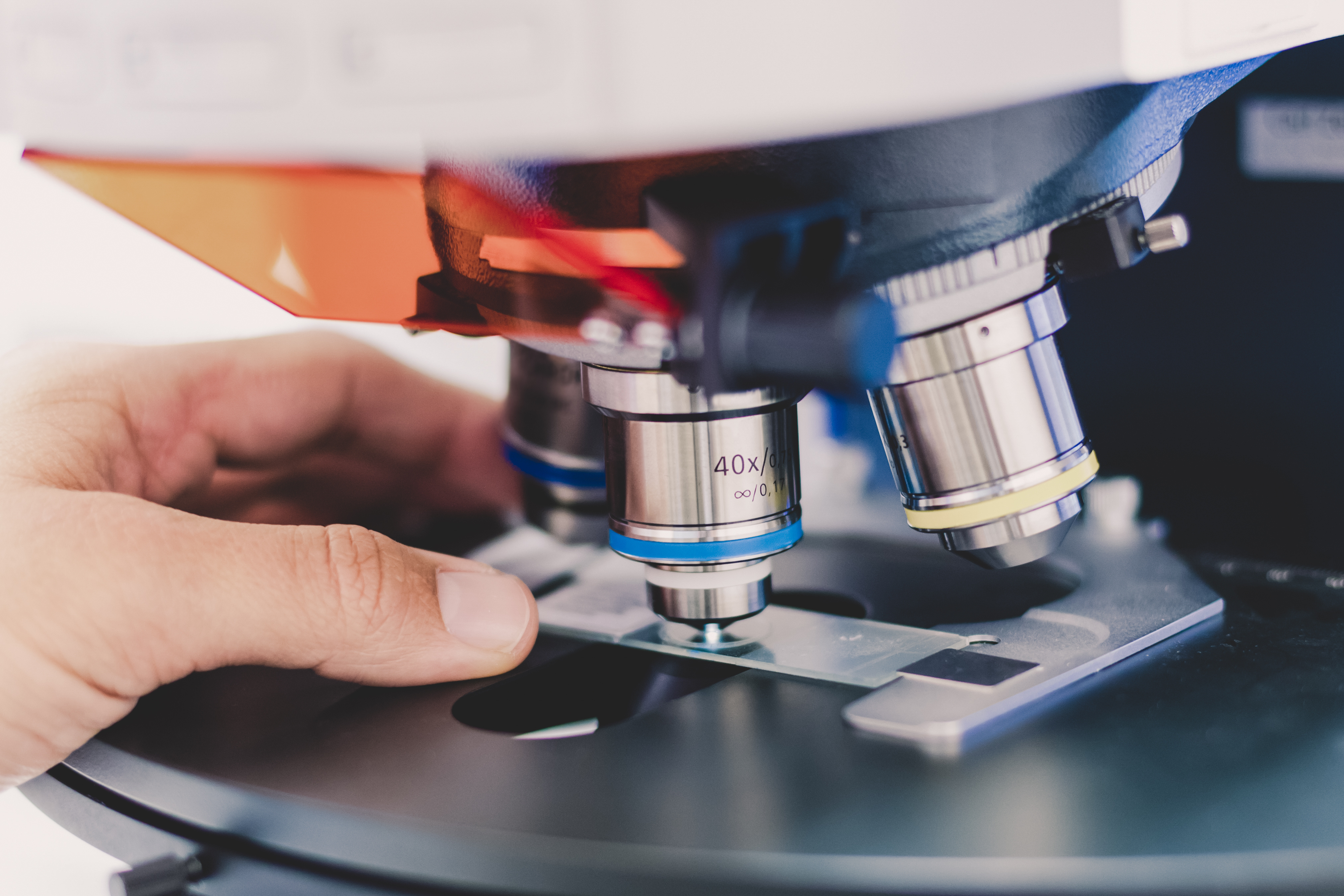
Evaluation methods include quantitative and qualitative assessments, alongside simulation testing. Standards for these evaluations draw from international, industry, and corporate benchmarks, laying the groundwork for a comprehensive appraisal of product reliability.
Through design refinement, material substitution, process enhancements, and stringent quality control, product reliability can be elevated, as evidenced by improvement measures and case studies.
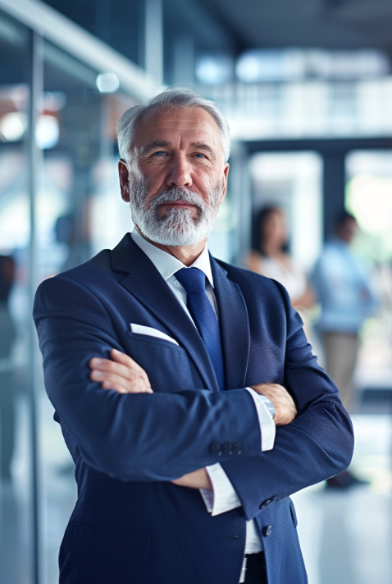
Regulations and standards establish clear-cut requirements for product reliability, including safety regulations, environmental demands, industry benchmarks, compliance certifications, recovery plans, and accountability measures. This ensures public safety and protects consumer rights. By adhering to these regulations and standards, companies can mitigate legal risks, boost market competitiveness, and foster consumer trust by offering highly reliable products.
Since 2018, MiFET has obtained International Organization for Standardization (ISO) certifications for Quality Management System (ISO 9001), Environmental Management System (ISO 14001) and Occupational Health and Safety Management System (ISO 45001). In the field of AMHS product technology system, we follow the standard communication protocols for semiconductor equipment, including SEMI E37, E82, E30, E84, E10, etc., so that it is easy to connect to semiconductor fab MES system to realize data interaction.